Grinding Wheel In Raw Mill Cement Plant
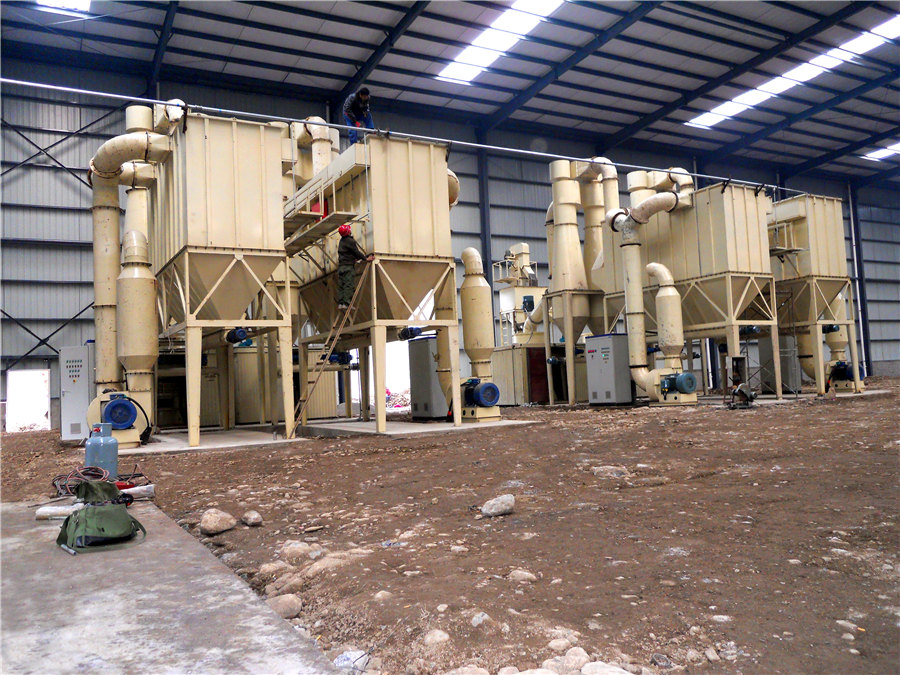
OK™ mill The most reliable and efficient mill for raw and
2023年8月17日 — The OK mill has proven to be effective for grinding blended cement with one or more wet components, because of its highly effective drying performance and its Closed circuit ball mill with two compartments for coarse and fine grinding and a drying compartment with lifters are generally found in cement plants for raw material grinding Raw Material DryingGrinding Cement Plant Optimization2017年8月12日 — For over 100 years the company Loesche has been building vertical roller grinding mills for grinding: Coal Cement raw material Clinker / granulated slag Industrial PROCESS OPTIMISATION FOR LOESCHE GRINDING 2021年1月1日 — Raw mix, high grade limestone, sand and iron ore are transported from their bins to raw mills for drying and further fine grinding The raw mill is either a Ball mill with Review on vertical roller mill in cement industry its
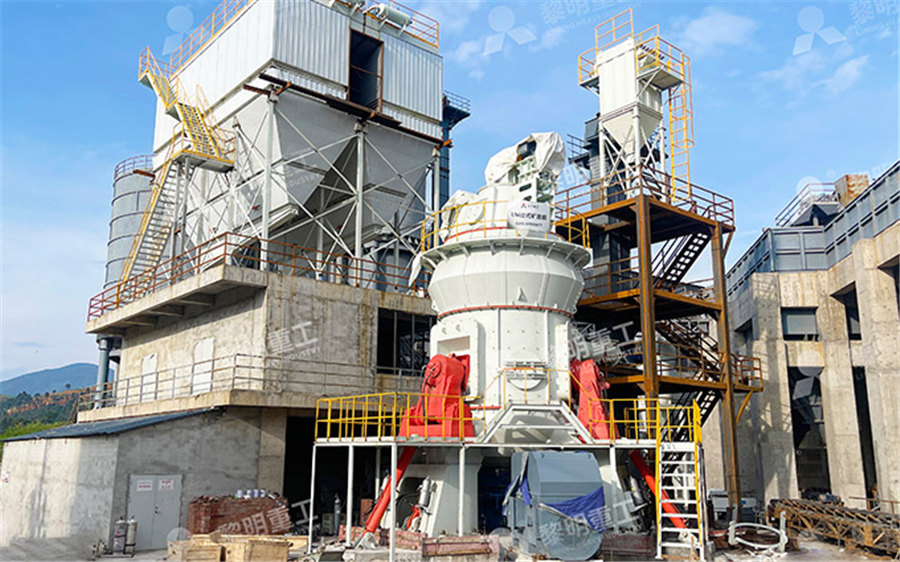
How Does A Raw Mill Work In A Cement Plant?
2024年6月18日 — Working principle: The material falls to the center of the grinding disc through the discharge pipe The grinding disc rotating at a constant speed uses the 2017年5月1日 — mills have been used successfully for the combined drying and grinding of cement raw material, coal, cement clinker, blast furnace slag and composite cements for many years(PDF) Grinding process optimization — 2014年4月1日 — The newly developed modular roller mill for grinding cement raw material, cement clinker, and additives with an installed power of up to 12,000 kW was specifically (PDF) The latest innovative technology for vertical roller mills 2017年6月19日 — Today's cement plants can now be designed with the onemill concept for both raw material and cement grinding The advantages of the modular vertical roller mill Grinding process optimization — Featuring case studies and
.jpg)
Vertical Roller Mill in Cement Manufacturing Plant
2023年7月4日 — A cement vertical roller mill (VRM) is a type of grinding equipment commonly used in cement plants for raw material grinding and cement grinding It is an energyefficient alternative to traditional ball Cement mill separator, or cement separator, is a type of equipment that was widely used in the cement grinding system and raw mill system of cement plantsThe function of the separator is to separate the finesized particles Cement Milll Separator Cyclone Air Separator in Vertical roller mill manufacturers Vertical roller mill or VRM is a largescale grinding equipment designed for pulverizing cement raw meal, cement clinker, slag, coal, fly ash, limestone, and other hard grinding materialIt integrates grinding, drying, separation, and conveying in one machine The equipment is widely used in many industries such as VRM In Cement Plant Maximize Energy Saving CNBM cement mills with a drying chamber see raw mills Mill working conditions: ventilation air speed through the mill Bigger or smaller than 12 [m/s] Material abrasivity The [%] of slag or pouzzolana content on the fresh Everything you need to know about
.jpg)
EnergyEfficient Technologies in Cement Grinding
2016年10月5日 — 1 Introduction Cement is an energyintensive industry in which the grinding circuits use more than 60 % of the total electrical energy consumed and account for most of the manufacturing cost []The requirements for the cement industry in the future are to reduce the use of energy in grinding and the emission of CO 2 from the kilns In recent Learn about the key features and benefits of vertical roller mills in cement plant operations Get expert insights and recommendations for optimizing your cement plant production with vertical roller mills where they are used to grind raw materials and clinker to produce cement The VRM technology has significantly improved the efficiency Vertical Roller Mill in Cement Plant ball mills supplier2 Raw Mill The raw mill is used to grind raw materials into “raw mix” during the manufacture of cement Equipment: Ball mills, vertical roller mills Technical Specifications: Ball Mills: 1030 tons/hour capacity, 5001500 kW motor power Vertical Roller Mills: 2050 tons/hour capacity, 10003000 kW motor power Example Brands:The Comprehensive Guide to Cement Plant Costs: An In Raw meal homogenization is the most important process link of the four, accounting for 40% of the homogenization task It is an important factor to support the balanced and stable working performance of preheaters and kilns, and plays an important role in improving the output and quality of cement clinkerHomogenization of Cement Raw Meal AGICO Cement Plant
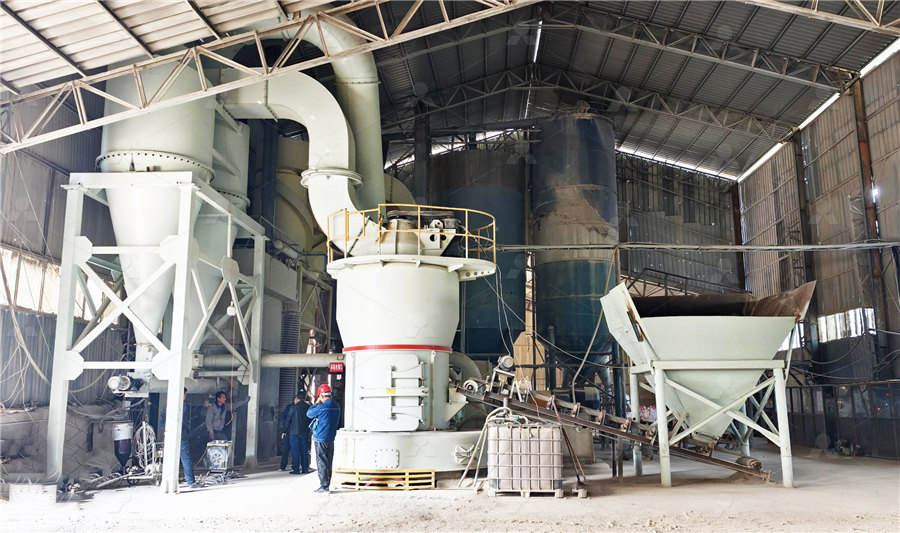
Bucket Wheel Stacker Reclaimer AGICO Cement Plant
Bridge Reclaimer The main difference in structure between the bridge bucket wheel stacker reclaimer and the portal bucket wheel stacker reclaimer is that it doesn’t has a tall portal frame; its bridge is fixed, and is in a lower position; there is no stacking belt conveyor and tail car; there is a material raking car in front of the bucket wheelThe stacker and reclaimer is the prehomogenization system in the cement plantAs a necessary part of the cement production line, it can concurrently or respectively complete the stacking and reclaiming The stacker and reclaimer play a vital role in the limestone prehomogenization, stabilize the condition of cement kiln, ensure the clinker qualityStacker And Reclaimer Cement Plant Parts2018年7月1日 — Benzer [13] studied on optimizing the fully airswept raw mill grinding circuit, Dundar et al [14] reported the optimization opportunities of a cement grinding circuit Altun and the chemical assays of the necessary samples were determined at cement plant by applying the standard procedures [18] 22 Mass balancing modelling studiesEnergy and cement quality optimization of a cement grinding circuit2017年8月12日 — vertical roller grinding mills for grinding: • Coal • Cement raw material • Clinker / granulated slag • Industrial minerals, and • Ores The core elements of these plants are the Loesche vertical mills for drygrinding the abovementioned grinding stock Loesche has developed and built the largest and mostPROCESS OPTIMISATION FOR LOESCHE GRINDING
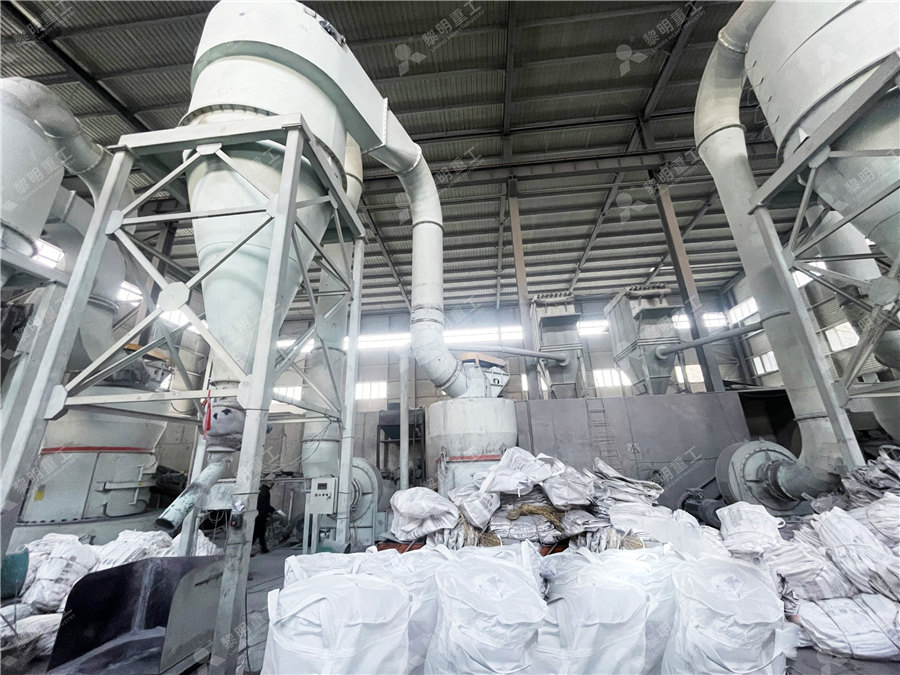
Cement Conveyor Belt Conveyor In Cement
Cement conveyor refers to a belt conveyor in cement plant, which is necessary accessory equipment in the cement production line A belt conveyor is a kind of material handling equipment with strong 2023年8月17日 — mill and an optimised spherical grinding profile for raw grinding applications The rollers are in a lifted position when the mill is started, ensuring troublefree startup A standard control system monitors the machinery and facilitates operation OK™ cement mill roller design OK™ raw mill roller design Quality and profitimproving featuresOK™ mill The most reliable and efficient mill for raw and 2023年8月21日 — In Udaipur Cement Works Limited, we use the following types of mills for grinding raw materials and cement: • Vertical Roller Mill (VRM): We employ the Loesche (LM 384) and Gebr Pfeiffer (MVR 6000C6) technology for raw material and cement grinding respectively which would either build new cement plants with the tech or retrofit old onesGrinding process is a critical stage in cement production2021年1月1日 — Raw mix, high grade limestone, sand and iron ore are transported from their bins to raw mills for drying and further fine grinding The raw mill is either a Ball mill with two chambers or Vertical roller mill with inbuilt classifier The hot gases from the pre heater enter the mill and are used for drying material in the millsReview on vertical roller mill in cement industry its
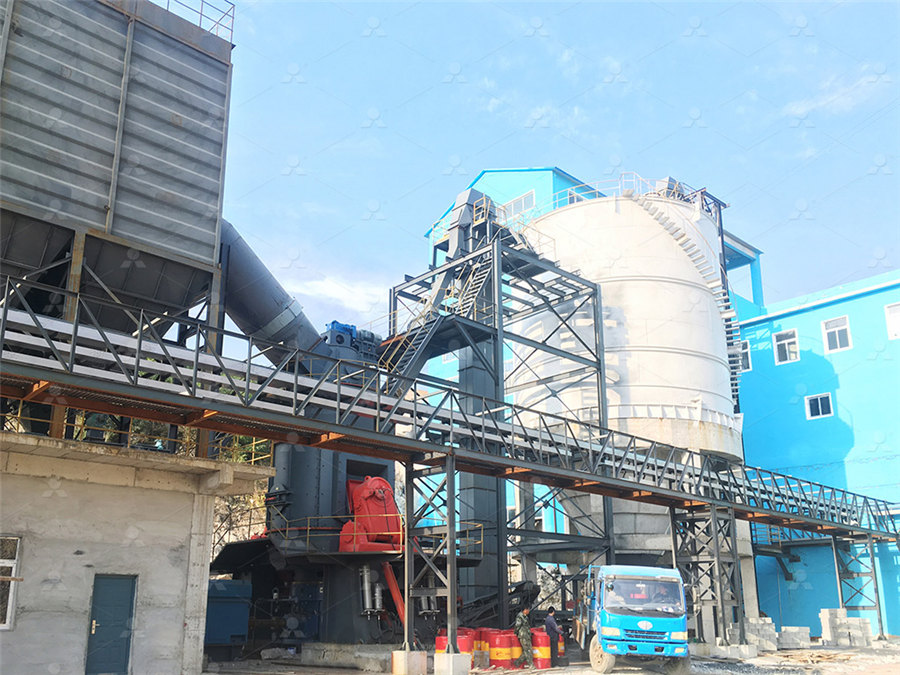
Application of Vertical Roller Mill in Cement Production
In the raw meal grinding process, VRMs are used to grind the raw materials used in cement production, such as limestone, clay, and silica After being crushed and processed in crushers,the raw materials are fed into the VRM through the center of the rotating table, where they are ground to powders by the rollersLearning outcomes An emphasis on the understanding of the milling technology system: Gas flow, advantage and disadvantage in the Raw mill and Cement mill installations – Grindability concept and the effects of intergrinding materials of different grindability – Ball mill grinding equations and dimensioning – Describe working principles for a separator – CEMENT GRINDING COURSE The Cement Institute2021年4月27日 — handled by the plant’s maintenance crew Upgrading the classifier and baghouse involves capital expenditure with a high benefit to cost ratio Optimization is especially important when multiple products are being produced Operation and Elements of a ClosedCircuit Ball Mill System Cement ball mills typically have two grinding chambersOPTIMIZATION OF CEMENT GRINDING OPERATION IN 2024年1月3日 — Grinding and separation efficiency of vertical roller mill were evaluated In addition to these, performance figures of vertical roller mill and conventional closed ball mill circuit were comparedPerformance Evaluation of Vertical Roller Mill in Cement
.jpg)
Cement Mill Separator High Efficiency Cement Separator
cement separator overview A cement separator is a key piece of equipment in cement production that focuses on removing oversized particles from the process air and making the finished product qualified It is primarily used in cement grinding plants at the cement mill outlet to separate fine particles from coarse particles A cement mill separator is also The cement roller press, also known as roller press in cement plant, high pressure grinding roll (HPGR), is a kind of cement equipment for brittle materials, apply for grinding cement clinker, cement raw material, Cement Roller Press, Roller Press In Cement The cement roller press is a type of materialcrushing machine which is often used in cement plants It usually works together with a ball mill to form a pregrinding or finalgrinding system for the grinding of raw materials, Hydraulic Roller Press in Cement Plants AGICO 2024年7月28日 — The raw mill of a cement plant prepares raw materials into raw materials that meet the requirements through steps such as crushing, mixing, grading (and possibly drying and sorting) In this process, the impact and rolling of steel balls (or grinding rollers) are the key to achieving raw material crushing and mixing At the same time, the use of How Does A Raw Mill Work In A Cement Plant? Baichy
.jpg)
Vertical Roller Mill in Cement Manufacturing Plant
2023年7月4日 — A cement vertical roller mill (VRM) is a type of grinding equipment commonly used in cement plants for raw material grinding and cement grinding It is an energyefficient alternative to traditional ball mills, as it utilizes rollers to grind and crush the materials between a rotating grinding table and a set of rollers mounted on a vertical axis2024年4月10日 — SINOMALY produces cement raw material grinding mills in various specifications These machines are suitable for grinding mill production lines with an output of 2500t/d, 3200t/d, 4000t/d, 5000t/d, 6000t/d and 8000t/d The vertical grinding mill is utilized for the grinding of raw materials, mixed cement, and slag powderVertical Roller Mill for Cement Raw Material SINOMALYBall mills in cement plants have a wide range of applications, including: Grinding of raw materials: The primary function of a ball mill in a cement plant is to grind the raw materials used in the production of cement These raw materials typically include limestone, clay, iron ore, and sometimes sandBall Mill In Cement Plant Selling Various Types Of Cement MillVertical raw mill is one kind of raw mill, generally used to grind bulk, granular, and powder raw materials into required cement raw meal in the cement manufacturing plantVertical raw mill is an ideal grinding mill that crushing, drying, grinding, grading transfer set in one It can be widely used in cement, electric power, metallurgy, chemical industry, nonmetallic ore, Vertical Raw Mill Cement Raw Mill Raw Mill In Cement Plant
.jpg)
Cement Roller Press Roller Press In Cement Plant Roller
In a cement plant, a cement roller press is a kind of important cement equipment used for clinker grinding It is usually combined with a cement ball mill to form a highefficiency cement grinding system because the practice shows that the grinding process with a small grinding ratio and stepbystep completion is more energysaving than that 2021年3月12日 — Ball mill optimisation As grinding accounts for a sizeable share in a cement plant’s power consumption, optimisation of grinding equipment such as ball mills can provide significant cost and CO 2 emission benefits to the cement producer n by Thomas Holzinger, Holzinger Consulting, Switzerland BALL MILLS 1 FEBRUARY 2021 INTERNATIONAL BALL MILLS Ball mill optimisation Holzinger ConsultingA coal mill is also called a coal pulverizer or coal grinder It is a mechanical device used to grind raw coal into pulverized coal powders The most used coal mills in cement plants are airswept ball mills and vertical roller mills At present, most cement plants use coal as the main fuel in the clinker production processCoal Mill in Cement Plant Vertical Roller Mill AirSwept Ball Mill2022年6月30日 — Cimencam (Holcim Group) will expand production at its plant in Figuil, in the north of Cameroon, and use Gebr Pfeiffer's energyefficient MVR mills for grinding raw material and cement The new Cimencam adds identical MVR mills for raw
.jpg)
Cement Grinding Unit Cement Grinding Plant
Equipment in cement grinding plant The cement grinding machine includes cement vertical mill, cement ball mill, cement roller press, cement seperator, conveyor and other cement equipmentWe can provide scheme design 2022年10月13日 — Besides, it might take two to three years to build up a cement plant The return on investment needs a longer time compared with the cement grinding plant The cement grinding investment is small and Differences Between Grinding Plant Cement Raw mill is also called cement raw mill, similar to cement ball mill, it is an important cement milling equipment used in the cement production process Raw mill is mainly used for grinding cement raw meal in the cement factory production process It is also suitable for metallurgical, chemical, electric power and other industrial mining enterprises to grind Cement Raw Mill in Cement Plant for Cement Raw Meal Grinding2022年10月3日 — For the past 2 onehalf years, in a cement plant in southern Germany, a singlecompartment raw grinding mill (4 8 m diameter, 10 m length) with preliminary size reduction and air separator drying (PDF) ANALISA KINERJA ALAT VERTICAL RAW MILL PABRIK II
.jpg)
(PDF) Performance Evaluation of Vertical Roller Mill in Cement Grinding
2017年9月11日 — The cement industry is the main supplier of raw materials for the production of concrete and reinforced concrete For grinding cement, two types of mills are used ball and rollerThese products are manufactured for cement plants, industrial gears wholesale, sugar mills, sag mills, ball mills, tube mills, coal mills, Raw Mill, Rod Mill, DRI Plant, Coal Plant, and sponge iron plants, grinding mills, gold mines, Power Plant, Pain Industries, Mineral Plants, Fertlizer Plant spare parts, Drier Drum, Granulator, Kiln Shell Roller Press For Grinding Mills Cement Plant IndiaMART2019年1月29日 — Raw Mill is mainly used to grind raw materials into fine powder, whereas Cement Mill is used for grinding clinker and other additives to form the final cement product The main difference between the two lies in their respective input materials; Raw mill mainly accepts raw materials from the kiln whereas Cement Mill mainly accepts precrushed What Is Cement Milling? Difference Between Raw Mill And Cement MillAll types of cement grinding mills such as cement ball mills, vertical roller mills, roller presses, and various related equipment form a highly efficient production line Closed circuit grinding systems equipped with an OSepa separator are more efficient especially when the grinding mill is a cement vertical millCement Grinding Units Cement Plant Equipment CNBM
.jpg)
Grinding Wheel In Raw Mill Cement Plant technesrl
Raw Material DryingGrinding Cement Plant Optimization Ball Mill Ball mills with high efficiency separators have been used for raw material and cement grinding in cement plants all these years Ball mill is a cylinder rotating at about 7080% of critical speed on two trunnions in white metal bearings or slide shoe bearings for large capacity Cement mill separator, or cement separator, is a type of equipment that was widely used in the cement grinding system and raw mill system of cement plantsThe function of the separator is to separate the finesized particles Cement Milll Separator Cyclone Air Separator in Vertical roller mill manufacturers Vertical roller mill or VRM is a largescale grinding equipment designed for pulverizing cement raw meal, cement clinker, slag, coal, fly ash, limestone, and other hard grinding materialIt integrates grinding, drying, separation, and conveying in one machine The equipment is widely used in many industries such as VRM In Cement Plant Maximize Energy Saving CNBM cement mills with a drying chamber see raw mills Mill working conditions: ventilation air speed through the mill Bigger or smaller than 12 [m/s] Material abrasivity The [%] of slag or pouzzolana content on the fresh Everything you need to know about
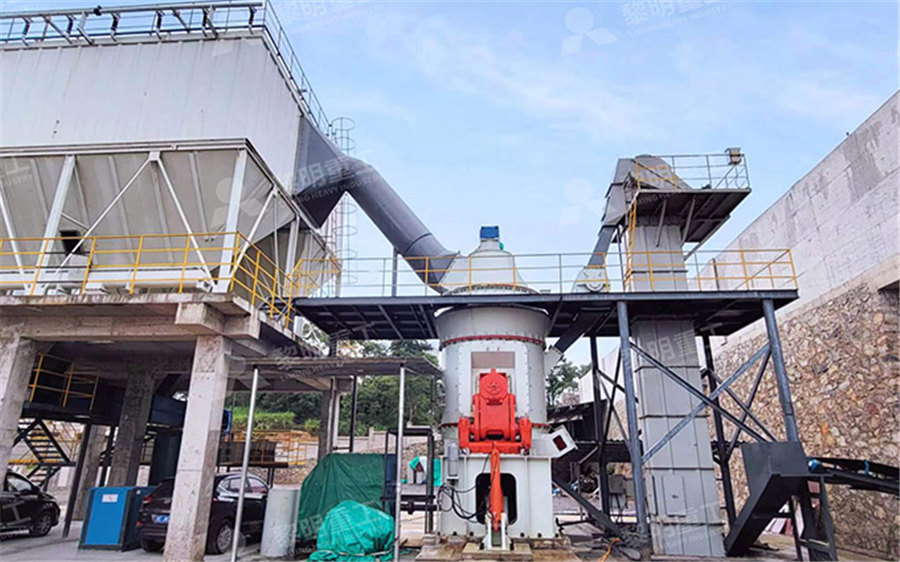
EnergyEfficient Technologies in Cement Grinding
2016年10月5日 — 1 Introduction Cement is an energyintensive industry in which the grinding circuits use more than 60 % of the total electrical energy consumed and account for most of the manufacturing cost []The requirements for the cement industry in the future are to reduce the use of energy in grinding and the emission of CO 2 from the kilns In recent Learn about the key features and benefits of vertical roller mills in cement plant operations Get expert insights and recommendations for optimizing your cement plant production with vertical roller mills where they are used to grind raw materials and clinker to produce cement The VRM technology has significantly improved the efficiency Vertical Roller Mill in Cement Plant ball mills supplier2 Raw Mill The raw mill is used to grind raw materials into “raw mix” during the manufacture of cement Equipment: Ball mills, vertical roller mills Technical Specifications: Ball Mills: 1030 tons/hour capacity, 5001500 kW motor power Vertical Roller Mills: 2050 tons/hour capacity, 10003000 kW motor power Example Brands:The Comprehensive Guide to Cement Plant Costs: An In Raw meal homogenization is the most important process link of the four, accounting for 40% of the homogenization task It is an important factor to support the balanced and stable working performance of preheaters and kilns, and plays an important role in improving the output and quality of cement clinkerHomogenization of Cement Raw Meal AGICO Cement Plant

Bucket Wheel Stacker Reclaimer AGICO Cement Plant
Bridge Reclaimer The main difference in structure between the bridge bucket wheel stacker reclaimer and the portal bucket wheel stacker reclaimer is that it doesn’t has a tall portal frame; its bridge is fixed, and is in a lower position; there is no stacking belt conveyor and tail car; there is a material raking car in front of the bucket wheelThe stacker and reclaimer is the prehomogenization system in the cement plantAs a necessary part of the cement production line, it can concurrently or respectively complete the stacking and reclaiming The stacker and reclaimer play a vital role in the limestone prehomogenization, stabilize the condition of cement kiln, ensure the clinker qualityStacker And Reclaimer Cement Plant Parts2018年7月1日 — Benzer [13] studied on optimizing the fully airswept raw mill grinding circuit, Dundar et al [14] reported the optimization opportunities of a cement grinding circuit Altun and the chemical assays of the necessary samples were determined at cement plant by applying the standard procedures [18] 22 Mass balancing modelling studiesEnergy and cement quality optimization of a cement grinding circuit